Makale, Odak Kimya tarafından sunulmaktadır
GİRİŞ
İçecek kutusu üretim endüstrisinde renk ölçümünün kullanımı oldukça yaygın ve uzun yıllardır yapılan bir uygulamadır. Bununla birlikte, bazı istatistiksel çalışmalar ve analizlerin sonuçları ve başarıları değişkenlik göstermektedir. Bu nedenle, renk ölçümünün standart olarak uygulanması ve endüstri tarafından benimsenmesi diğer ambalaj sektörlerine göre daha düşüktür.
Renk ölçümünün daha az benimsenmesinin nedenlerinin çoğu, verilerin yorumlanmasında temel bir bilgi eksikliğine dayanmaktadır ve bu, ilk bakışta görsel ve dijital kabul arasında bir anlaşmazlık gibi görünebilir.
Renk ölçümü, içecek kutusu endüstrisinin devam eden gelişiminde ayrılmaz bir rol oynayacak şekilde düzenlenmiştir. Renk standartları için dijital verilerin kullanılması yalnızca daha tutarlı, daha doğru bir üretim sağlamakla kalmaz, aynı zamanda tasarımın ve baskının daha hızlı yapılmasının ve renk iletişiminin daha verimli olmasının da anahtarıdır.
Renk ölçümünün doğru şekilde kullanıldığından emin olmak için, uygun prosedürlerin ve tekniklerin kullanılması ve verilerin uygun şekilde değerlendirilmesi çok önemlidir.
Renk Uzmanları tarafından hazırlanan bu makale aşağıdaki konuları açıklayacaktır:
- Üretim değişkenlikleri nasıl renk sorunlarına yol açabilir?
- Neden görsel değerlendirme bu sektör için tek başına yetersizdir?
- Renk ölçüm araçlarını kullanırken en çok karşılaşılan sorunlar.
- Speküler dahil ve speküler hariç ölçüm verileri arasındaki farklar ve hangilerinin kullanılacağı.
- Renk kabulünü hem görsel hem de dijital olarak uyumlu hale getirmek için doğru tolerans yöntemi nasıl seçilir?
İki Parçalı Kutular için Üretim Değişkenleri
Konserve endüstrisinde birçok hareketli parça ve değişken vardır. Ürünlerin bütünlüğü için gerekli olan ve nihai görsel yönüne katkıda bulunan sofistike mühendislik adımlarını içerdiğinden, kutu yapımı sadece basit bir baskı süreci değildir.
Kutu, hayatına bobin olarak sarılmış dev bir düz levha alüminyum olarak başlar. Küçük kaplar bobinden kesilerek alınır ve belli belirsiz bir teneke kutuya benzeyen bir silindir oluşturmak üzere gerilir. Bu silindir traşlanır, temizlenir ve bir atom kalınlığında Zirkonyum tabakası ile kaplanır. Kutu daha sonra, kutunun dekorasyon aşamasına sorunsuz geçişini sağlamak için genellikle bir yağlayıcı ile kaplanır. Ayrı kalıplardan bir blanket üzerine ve ardından kutuya sekiz adede kadar mürekkep baslır. Mürekkepler daha sonra yaş üstüne yaş olarak bir vernikle kaplanır ve 200 santigrat derece sıcaklıklarda hemen kürlenir. Daha sonra kutunun içi spreyle kaplanır ve yaklaşık 200 santigrat derece sıcaklıkta yeniden kürlenir. Son olarak, boyun çok aşamalı bir işlemle oluşturulur. Tüm bunlar, üretim hattı başına dakikada iki bin kutu hızında işlenir. Birçok hat, haftanın yedi günü, günde yirmi dört saat çalışır.
- Üretim Değişkeni: Vernik Gramajındaki Değişiklikler
Vernik, bir aplikatör silindiri kullanılarak doğrudan yaş mürekkebin üzerine uygulanır. Teneke kutu/mürekkep yüzeyinin tamamen kimyasal ve mekanik bir bariyerle kaplandığından emin olmak için üst üste binen vernik uygulanır. Örtüşmenin boyutu ve konumu, makine kurulumuna ve tipine göre değişir. Bu örtüşme işlevsel bir gereklilik olsa da parlaklık, opaklık ve renk açısından değişkenler getirir ve dE 1,5’e kadar bir değişim yaratabilir.
- Üretim Değişkeni : Vernik Cinsi
İki parçalı içecek endüstrisinde kullanılan vernik ürününün türü, müşteri ihtiyaçlarına, çevresel faktörlere ve proses kısıtlamalarına göre değişebilir. Örneğin, bölgenin dolum veya taşıma ihtiyaçlarına bağlı olarak daha yüksek düzeyde aşınma direnci gerekebilir. Bu özelliği iyileştirmenin bir yolu, formülasyondaki wax (mum) seviyesini arttırmaktır. Bununla birlikte, daha standart, şeffaf bir ürünle karşılaştırıldığında, görsel etkisi daha fazla opaklıktır. Opaklıktaki bu artış bazı koyu renklerin daha zayıf görünmesine neden olabilir. Mürekkep film kalınlığı artırılarak bu durum önlenebilir; bununla birlikte, bunun yine de speküler hariç yapılan ölçümde daha fazla değişim göstermesi muhtemeldir. Mürekkep formülasyonuna bağlı olarak, bu değişiklik iyileştirilemeyebilir.
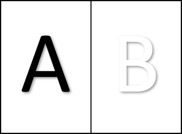
- Üretim Değişkeni : Baskı altı malzemesi
Mekanik ve kimyasal işlemler nedeniyle, alüminyum baskı altı malzemesinin özelliği değişebilir. En çok görülen değişimler, yüzeyin yansıtıcılığının daha da artması veya azalması ile yüzeyin basılabilirlik özelliklerindeki değişimdir. Renk görünümü açısından bu durum, opaklık, parlaklık (temizlik) veya renk şiddetinde değişiklikle sonuçlanabilir.
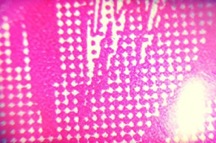
Görsel ve Dijital Karşılaştırmaların Tutarsızlığına Katkıda Bulunanlar
Katkıda Bulunan 1: Düz ve Yuvarlak Örnekler
Kutunun yansıtıcı doğası ve yüzeyinin silindirik olması nedeniyle, yüzey düz haldeyken ölçülen renkler ile silindirik halde ölçülen renkler karşılaştırıldığında ölçüm sonuçları dE 1.0 kadar veya daha fazla değişebilir. Bu nedenle, renk standardının nasıl ölçüldüğünü bilmek ve ölçüm yaparken tutarlı bir süreç sürdürmek önemlidir.
Renkleri kutu düz haldeyken ölçmenin daha iyi olabileceği düşünülürken, özellikle üretim ortamında silindirik haldeyken ölçüm yapmak genellikle daha pratiktir. Daha da önemlisi, silindirik haldeki ölçüm, son kullanıcının görüşü ile daha iyi uyum sağlayacaktır çünkü nihai ürün bu şekilde görüntülenecektir.
Kutunun deformasyonunu önlemek ve boyunsuz bir içecek kutusunun ölçümlerini tutarlı olarak yapmak için bir aparat gereklidir. Aşağıda, X-Rite Ci60 serisi spektrofotometrenin kutuyu silindirik bir şekilde, bozulma olmadan birden çok yönde ölçebilmesi için kutuyu sabit bir şekilde tutan uyarlanabilir bir aparat bulunmaktadır.
Şekil 3: İçecek kutusu tedarikçilerinde, X-Rite’ın bardak ve hassas silindir ölçüm aparatı bulunmaktadır. Böyle bir aparatın temel tasarım unsuru, ölçüm sırasında spektrofotometre ve kutunun dairesel olarak temas halinde olmasıdır.
Katkıda Bulunan 2: Ölçüm Yönü
Cihazın ölçülecek numuneye göre ölçüm yönünün hep aynı olması, özellikle silindirik bir kutudan veya ondan kesilmiş numuneleri ölçerken çok önemlidir. Bir rengi görmenin doğru ya da yanlış bir yolu yoktur. Ancak, cihazı 90 derece döndürdükten sonra metal üzerindeki bir baskı alanını ölçerken ortaya çıkan renk farkı önemli olabilir.
Düz bir numuneden ölçüm alırken, farkı azaltmak için birden fazla açının ortalamasının alınması şiddetle tavsiye edilir. Rengi karakterize etmenin ve görsel yönüyle ve tipik görüntüleme koşullarıyla iyi uyum sağlayan verileri oluşturmanın pratik bir yolu, bir ölçüm yapmak, cihazı 45 derece döndürmek ve başka bir ölçüm yapmak, ardından bunu başka bir 45 derecelik dönüşle tekrarlamaktır.
Aşağıdaki fotoğraflar, yuvarlak numunenin farklı yönlerdeki renklerinin doğru ölçümü için kullanılan yöntemi göstermektedir.

Katkıda Bulunan 3: Speküler Dahil Edilen ve Speküler Hariç Tutulan Veriler
Toleransın belki de en önemli kısmı, speküler dahil edilmiş verileri, speküler hariç tutulan verileri veya her ikisini birden kullanmaktır.
Speküler dahil, rengin parlaklık özelliğini de hesaba katarak karşılaştırma yaptığından, en yaygın olarak kullanılan yöntemdir. Nadiren speküler hariç tutulan veriler kullanılır. Bazıları parlaklığın kutu üretim sürecinde nispeten kontrol edilemez bir unsur olduğuna ve bu nedenle, bu değişkeni kaldırarak mürekkep filmi kalınlığının ölçülmesinin daha kontrol edilebilir olduğuna inanmaktadır. Ancak, bu argüman hatalıdır.
Yansıtan veya yansıtmayan olarak hem speküler dahil hem de speküler hariç ölçüm şekillerini birlikte düşünmek en iyisidir. Her iki ölçüm şeklinin kullanılması, yansıtıcılığı değişken bir yüzey üzerine basılmış rengin daha iyi değerlendirilmesini sağlayacaktır. Aslında, speküler dahil veya speküler hariç olarak yapılan ölçümlerde mükemmel bir dijital eşleşme elde edilirken, görsel olarak yapılan karşılaştırmada tam bir uyumsuzluk ile karşılaşılabilir.
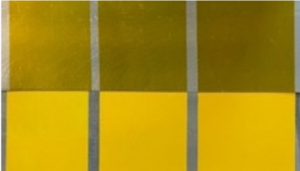
Sonuç olarak, doğru opaklık ve görsel renk eşleşmesini elde etmek için bir tolerans ayarlarken hem speküler dahil edilen hem de speküler hariç tutulan bileşenler birlikte kullanılmalıdır.
Anlamlı Bir Tolerans Seçmek
İki parçadan oluşan içecek kutusu üretim sürecindeki çeşitlilik göz önüne alındığında, anlamlı bir tolerans belirlemek zor görünebilir. Bununla birlikte, birden fazla tesis, firma, üretim çalışması ve stok kodunda rengi kontrol etmek için yalnızca görsel yöntemleri kullanmaya çalışmanın yetersiz olduğu defalarca kanıtlanmıştır.
Özellikle renk onayı görsel olarak verilse bile, mevcut piyasa standartlarının yüksek olduğunu akılda tutmakta fayda vardır. Ayrıca, olası tüm süreç varyasyonlarının kümülatif olduğunu ve iyileştirme seçenekleri sunmadığını varsaymak bir yanılgıdır. Bir değişken, sorunu karmaşıklaştırmak yerine diğerini dengeleyebilir.
Örneğin, uygulanan vernik gramajı ortalama değere kıyasla biraz düşükse, normal olarak, vernik gramajı arttırılarak düzeltilecektir. Ancak çeşitli nedenlerle uygulanan vernik gramajını arttırmak pratik olmayabilir. Bunun yerine, basılan mürekkep miktarını artırmayı seçmek, daha kabul edilebilir bir görsel eşleşme ve daha iyi dijital değerler sağlayabilir.
1 – Bitmiş İçecek Kutusu İçin Tolerans Ayarlama
- dE 2000 = 0 Speküler Dahil, D50/20
- dE 2000 = 3,5 Speküler Hariç, D50/20
Seçilen toleranstan bağımsız olarak, endüstri dijital renk yönetiminin daha fazla benimsenmesine uyum sağladığından, bu tolerans bir başlangıç noktası olarak belirlenebilir. Gelişmeler oldukça, bunu bir hedef olarak kullanmaktansa, kalitenin sürekli olarak geliştirilmesinin zorunlu olduğu kabul edilmelidir.
2 – Renk Eşleştirme için Tolerans Ayarlama
- dE 2000 = 1,5 Speküler Dahil D50/20
- dE 2000 = 0 Speküler Hariç D50/20
Renk eşleştirme için bir tolerans belirlemek tartışmalı bir konu olabilir. Teneke kutu üreticisinin bakış açısından, renk eşleştirme için seçilen dE değeri ne kadar düşükse, teneke kutu üretimi için çalışma penceresi o kadar geniş olur. Bununla birlikte, potansiyel baskı altı malzemesi ve vernik kısıtlamaları göz önüne alındığında, bitmiş ürün anlamında çok düşük bir dE değeri elde etmek mümkün olmayabilir.
Numune üretiminde elde edilen dE değerinin üretimde elde edilebilecek en olası sonuca eşit olacağını varsaymak da çok karşılaşılan bir yanılgıdır. Bununla birlikte, yukarıda özetlendiği gibi bazı üretim süreci değişkenlerini ayarlayarak farklılıklar potansiyel olarak dengelenebileceğinden, üretimdeki sonuçlar numune üretiminden daha iyi olabilir.
3 – Tolerans Değişkenlerini Anlamak
Bir renk ölçümü toleransları aşarsa, dE değerinin neden yüksek çıktığını anlamak önemlidir. Bu yüksek dE değeri, speküler dahil veya speküler hariç bileşenler tarafından oluşuyorsa, veya her ikisinden de dolayı değilse, bu muhtemelen opaklık veya reflektansdaki bir farktan kaynaklanmaktadır. Bu, vernik veya baskı altı malzemesinin bir kısıtlaması olabilir. Alternatif olarak, fark, yine vernikle veya baskı altı malzemesinin basılabilirlik özelliğinden dolayı elde edilen renk şiddeti ile ilgili olabilir.
Bu noktaların tümü, verilerin anlaşılması ve çevrilmesi ile ilgilidir. Renk ölçümü tarafından sunulan veri ve bilgilerin, durumun gerçek bir ifadesinden daha fazlası olarak alınması gerekir. Bir bütün olarak alınmalıdır. Verilerin yalnızca bir kısmının kullanılması yanlış yorumlamalara ve yanlış önlemlerin alınmasına neden olabilir. dE dışındaki verileri de kullanmak, daha hızlı, daha etkili düzeltici eylemler yapılmasını sağlar.
Özet
İçecek kutusu endüstrisinde renk ölçümü daha da önemli bir rol oynamaya devam ederken, dijital verilerin kullanılması tutarlı renk iletişimi, doğru üretim, daha hızlı tasarım ve daha verimli baskı süreleri için bir çözüm sunmaktadır. Ancak, uygun prosedürleri ve teknikleri kullanmak ve verileri uygun şekilde değerlendirmek çok önemlidir.