Probo, a trade printer with facilities in the Netherlands, Belgium, and Germany, is a business with innovation at its core. Founded in 2001 in the Netherlands, Probo, originally Probo Sign, focused on lettering and engraving, and in 2007, implemented its unique reseller model that made high-tech printing accessible to all print professionals. International expansion, investment in sustainable solutions, and technological advancements followed, and today Probo supports more than 12,000 print professionals, operates more than 25,000 m² of production space, and offers more than 300,000 product combinations on over 280 materials.
As Probo continues to grow, it’s important that the investment in new machinery is in keeping with their innovative approach. “Probo’s approach to selecting new equipment aligns with the principles of Industry 5.0, where automation, human creativity, and sustainability intersect to create a smarter and more efficient production environment,” says Jordy de Jong, Marketing and Business Development Manager, Probo. “This focus on future-proof technology reflects Probo’s mission to empower print professionals and lead the way in manufacturing Industry 5.0—a smarter, more sustainable print industry built on innovation and collaboration.”
Experiencing automation in action
When Probo first discovered PLASTGrommet’s finishing solutions, they were looking at ways to boost capacity in order to deliver products to customers faster and at a better price. “We first encountered PLASTGrommet at FESPA 2021 in Amsterdam,” says Jordy. “After seeing the All In One machine in action, we were very interested, and started the quotation process.” The All In One from PLASTGrommet is a cutting-edge automated solution for large-format banner finishing, seamlessly integrating welding, eyeleting, and cutting into a single efficient process. Designed with productivity in mind, the All In One reduces lead times and labour costs while conserving valuable floor space. Key features include an automatic roll edge alignment system, a vision system for precise eyelet and cut mark reading, and industrial-grade hot air welders capable of 24/7 operation.
In 2022, Probo took delivery of the All In One at its Dokkum location, and haven’t looked back since. Probo’s All In One configuration offers a choice of four fixed formats; 100cm, 150cm, 175cm, and 200cm, and gives customers the option of a hemming or hemming and rings finish. “Over the years, I’ve overseen many installations and implementations, and I can confidently say that the installation and implementation of this project was among the best,” says Jordy. “Communication from PLASTGrommet was very strong and well structured. They were extremely eager to get everything right the first time. There were thorough training sessions for both the operators and the technical team.”
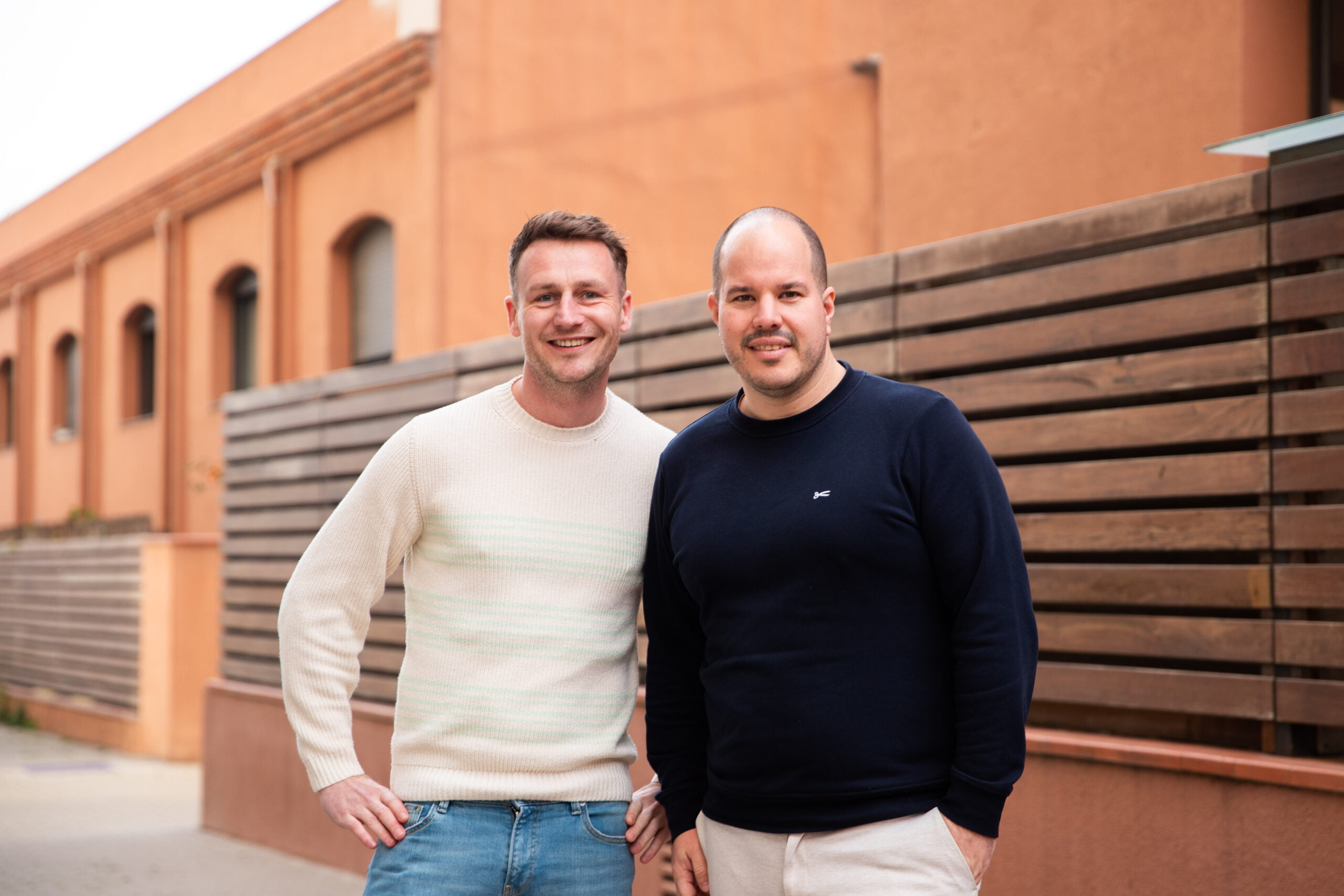
Outlining the seamless workflow integration process, Jordy continues: “Orders from Probo.nl that qualify for the All In One are automatically intercepted from Pre-press, with the platform recognising the standard widths. The orders are then collected and grouped by standard banner width. Afterward, our planning team schedules the orders on a specific printer, and the printed roll goes to the All In One. The machine is directly connected to a manual hemming and eyeleting machine, allowing us to efficiently finish the short sides of the fence banners.
“PLASTGrommet provides timely and effective support, ensuring their technology runs seamlessly in our production. Their proactive communication, quick issue resolution, and expert guidance help us maintain the high standards our print professionals expect. This reliable partnership strengthens our ability to deliver quality, speed, and innovation.”
Targeting new markets with All In One
Since instalment, Probo’s experience with the All In One from PLASTGrommet has continued to reap benefits, as Jordy explains: “The investment in the PLASTGrommet finishing machine has significantly impacted Probo’s business by increasing the share of wallet with our existing print professionals. Previously, print professionals relied on Probo for low-volume barrier banners, thanks to our flexibility and quality. With the introduction of the All In One, we are now able to offer competitive solutions for high-volume orders as well. This dual capability—serving both low and high volumes—ensures that customers can consolidate all their barrier banner needs with Probo, rather than sourcing high volumes elsewhere.”
The positive impact of the All In One is evident from the customer response. Previously, many Probo customers expressed regret that they could not order high-volume barrier banners at a desirable price point. “The market for construction banners has experienced a huge growth. A lot of print professionals are buying these products in high volume in low wage countries, and at Probo we believed we could provide better products for this market.Probo has received enthusiastic feedback from customers regarding the benefits of the PLASTGrommet finishing machine,” says Jordy, adding: “With this new capability, customers are now thrilled to consolidate all their orders with Probo. We’ve seen a significant improvement in lead times, enabling us to guarantee delivery times for our customers.”
A sustainable future for print
Minimising waste across the value chain with smart production techniques is at the forefront of Probo’s principles. In 2022, the company reinforced its commitment to circular innovation, launching Sign Again, the first 100 percent circular material made entirely from used banners and cutting waste. “With local, on-demand production and circular solutions like Sign Again, we minimise environmental impact while maintaining the highest quality standards,” Jordy explains. In 2024, Probo unveiled “Het Kompas,” its roadmap for innovation and sustainability, kicking off construction on a fully automated warehouse and giving Sign Again its own dedicated production space.
The relationship with PLASTGrommet has played a crucial role in Probo’s sustainability strategy, as Jordy details: “One standout benefit of working with PLASTGrommet is the ability to use PVC-free plastic rings in our finishing process. This feature is crucial for simplifying the recycling of banners into Sign Again, our circular material. This aligns perfectly with Probo’s mission to lead the way toward a circular print industry, reducing waste and creating sustainable solutions for the future. PLASTGrommet’s equipment not only enhances efficiency but also supports our commitment to innovation and sustainability.”
Continuing on a prosperous path
Since the relationship’s inception, the two companies have worked closely to highlight the synergy between Probo’s print production process and PLASTGrommet’s equipment, including at FESPA 2024 in Amsterdam, in a city in which Probo and PLASTGrommet first became acquainted at the 2021 show, where Sign Again was highlighted on the PLASTGrommet stand. Jordy says: “This partnership shows how we collectively work toward a sustainable, innovative, and future-proof print industry—one that balances technology, creativity, and environmental responsibility.”
Looking ahead, as Probo always does, the relationship between Probo and PLASTGrommet is set to continue to thrive. “We continue to focus heavily on automation, robotics, and AI, as these technologies drive efficiency, scalability, and sustainability. Any innovation that aligns with these priorities, including advancements from PLASTGrommet, is of great interest to us. We see PLASTGrommet as a valuable partner, and further investments in their technology are always on the table if it supports our mission of delivering cutting-edge solutions for our print professionals,” says Jordy.